Narrowing Discrepancies in Industrial Production guided by Data Analysis
** Streamlining Manufacturing Decisions: Unleashing the Power of Data-Driven Insights**
In today's cutthroat manufacturing landscape, data-driven decision-making is the key to success. Customers' quest for affordability and quality, coupled with the pressure for timely deliveries, leaves little room for error and old-school tactics. Instead, well-run manufacturers rely on data-backed insights gathered from their front-office and shop-floor operations to make informed decisions.
Yet, despite the widespread acceptance of data-driven manufacturing principles, a recent survey by Dassault Systèmes revealed that 20% of manufacturers frequently make poor decisions due to unavailable, unreliable, or inaccessible data. On the flip side, the survey showed that 70% or more respondents reported significant improvements in areas like quality, production efficiencies, and sales when manufacturing data was reliable and easily accessible.
Ensuring end-to-end control and visibility over the manufacturing process, from sales order to shipment, requires bridging the data gaps that often exist between front-office planning operations and actual production execution, quality assurance, and warehousing. The secret to success lies in planning well and being aware of any production delays or quality issues that may derail plans, allowing for swift corrective action to prevent minor problems from snowballing into significant delays.
Take SAY Plastics, for example. By leveraging their ERP system's dashboard, advanced production tracking, and alert systems, SAY Plastics can monitor production timelines and quickly identify bottlenecks, adjust schedules as needed, and optimize resource allocation to meet deadlines. Real-time data helps the company address any issues in the supply chain, resulting in a dramatic improvement in on-time delivery rates that now are as high as 99%.
In the survey, deficiencies in production performance and quality control were the most frequently reported gaps. These areas often see isolated management systems decoupled from the organization's primary manufacturing operating system. Closing these data gaps necessitates integrating the results from production monitoring, process monitoring, and quality inspections into the information flow that informs the front-office planning and customer relations teams.
SIGN Fracture Care, an FDA-registered and ISO 13485-certified medical device manufacturer, offers a shining example of how to close the quality control-to-the-rest-of-the-organization divide. By automating its quality control processes using the ERP system and digitizing inspection data storage, SIGN improved regulatory compliance and maintained comprehensive device history records.
Production monitoring tracks a work order's progress through the production phase, while process monitoring verifies whether tooling and equipment meet specifications. Without real-time production, process, and quality data, planners risk scheduling jobs and materials into work centers that are still occupied by a prior production task, compounding problems. A closed information loop that connects shop-floor results with front-office software, however, empowers planners to realistically schedule resource allocation, ensuring efficient production and minimizing delays.
Manufacturers are, therefore, focusing considerable operational and information technology resources on connecting their ERP, manufacturing execution, and quality assurance systems, either through systems integration or adopting platforms with native integration of these disciplines.
Data-Driven Decision Making in Action
With Integrated planning, production, and quality data, manufacturers can improve performance in key areas:
Quality Control (47%): Real-time quality inspections prevent defects from becoming systemic and provide data for statistical process control (SPC) analysis and customer documentation.
Business Strategy (43%): Accurate cost data, driven by shop floor monitoring, helps identify profitable products, necessitate price updates, and reveals valued customers for strategic management.
Customer Service/Support (36%): ERP systems provide fact-driven delivery time frames to customers, improving transparency and customer satisfaction.
Operator Performance (34%): By using production and process monitoring to track cycle times, managers can assign jobs based on actual performance data, streamlining production and reducing waste.
Order Management (32%): Real-time data enables manufacturers to optimize production schedules, identify resources that need to be expedited, and prevent late deliveries or costly rush fees.
Many manufacturing businesses still struggle with information gaps resulting from error-prone manual record-keeping and fragmented information systems. By bridging these data gaps and connecting their ERP, manufacturing execution, and quality assurance systems, manufacturers can achieve real-time closed-loop data, empowering them to make data-driven decisions proactively, improve performance, and stay competitive in today's fast-moving manufacturing landscape.
- To optimize manufacturing processes and deliver quality products on time, manufacturers are focusing on unifying their ERP, manufacturing execution, and quality assurance systems.
- Real-time data integration simplifies planning by enabling real-time production scheduling, identifying bottlenecks, and adjusting resource allocation to ensure efficient operation.
- Quality control improvements are possible with real-time quality inspections, which prevent defects from becoming systemic and provide data for statistical process control analysis.
- Accurate cost data, driven by shop floor monitoring, assists in identifying profitable products, necessitating price updates, and revealing valued customers for strategic management.
- Transparency and customer satisfaction can be improved by providing fact-driven delivery time frames to customers through ERP systems.
- By tracking cycle times and using production and process monitoring, managers can assign jobs to operators based on actual performance data, streamlining production and reducing waste.
- Real-time data enables manufacturers to optimize production schedules, identify resources that need to be expedited, and prevent late deliveries or costly rush fees, thus contributing to sustainable living and technology advancement within the manufacturing industry.
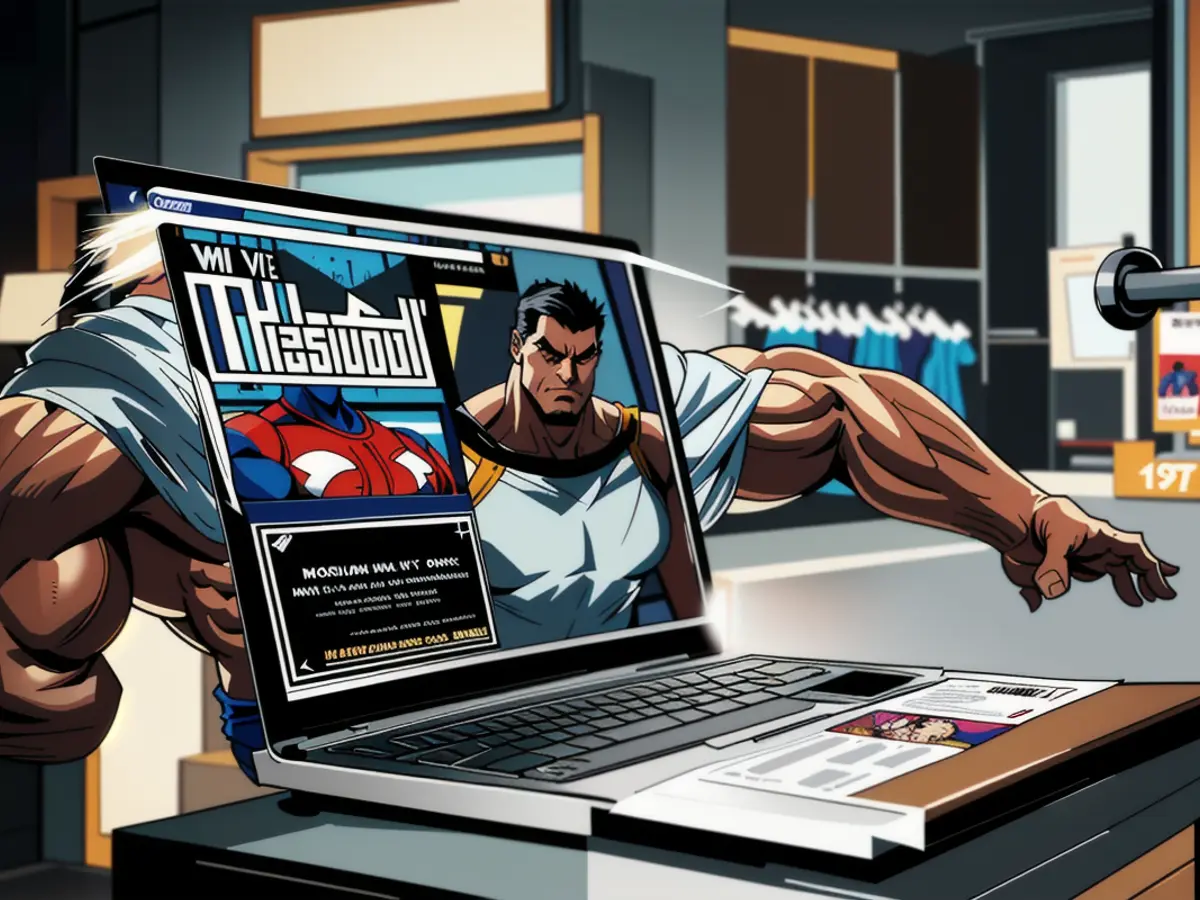
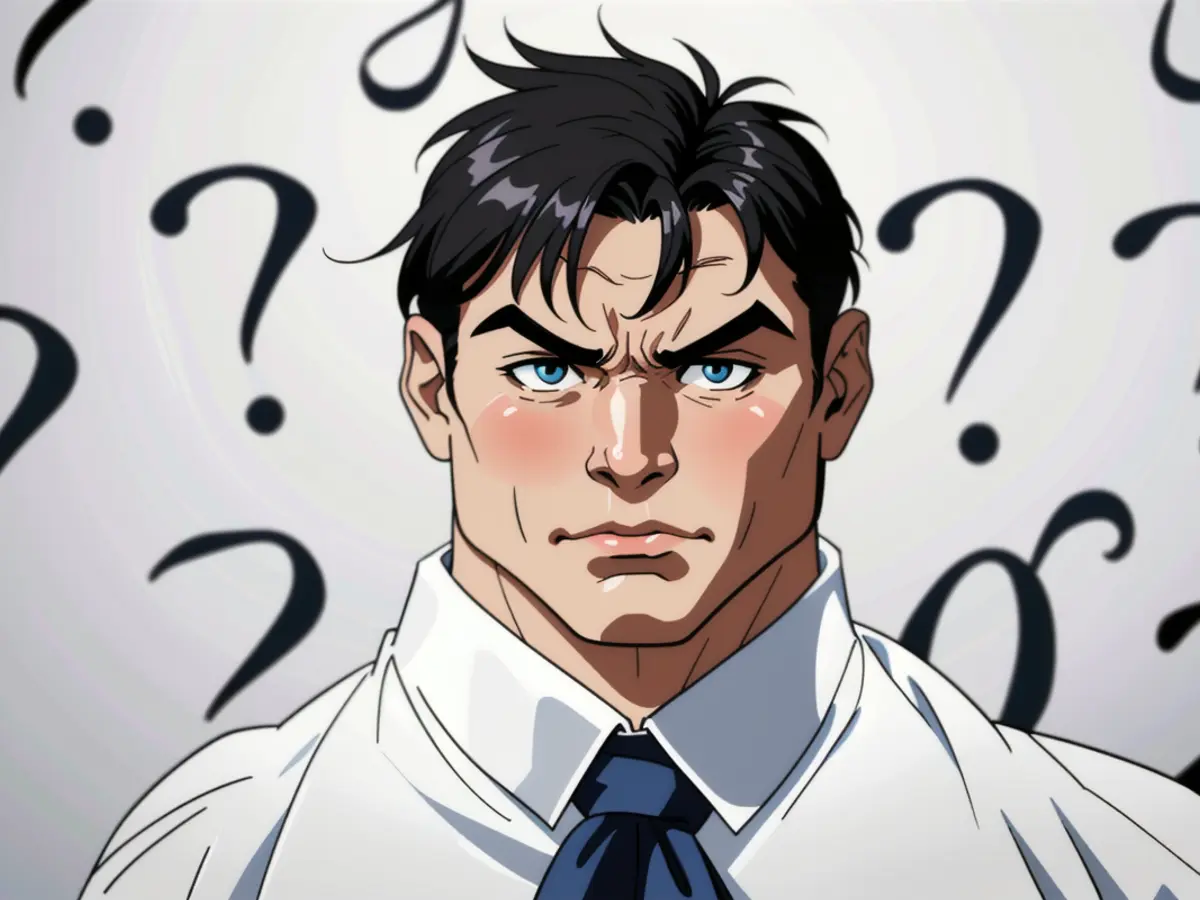
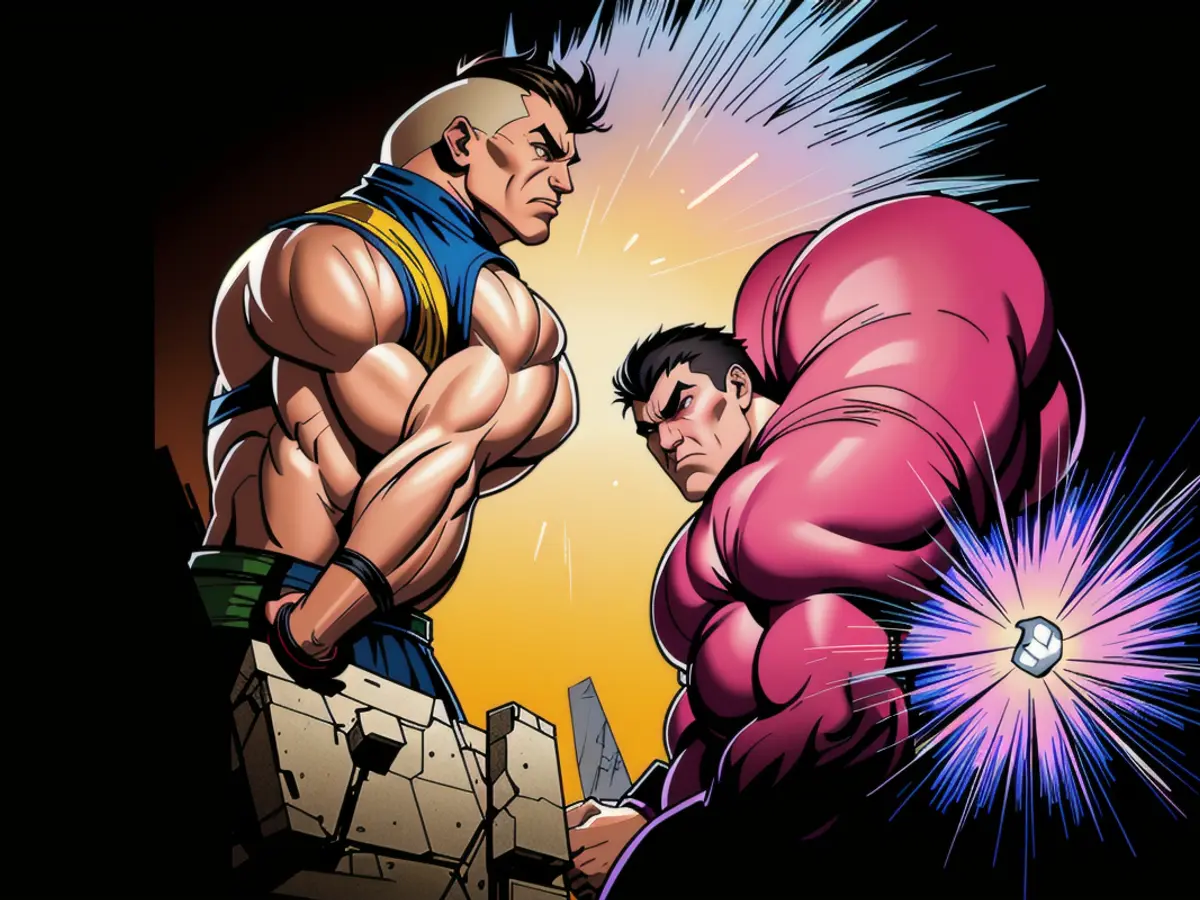